OT: Herr Jaeger, welche Erfahrungen haben Sie mit additiven Herstellungsverfahren gemacht?
Martin Jaeger: Wir haben bereits 2004 mit 3D-Scans angefangen. Das hat von Anfang an ganz gut geklappt. Den ersten D‑Drucker haben wir 2016 angeschafft, allerdings mit mäßigem Erfolg. Für 400 Euro hatte ich den Drucker im Internet bestellt und ihn nie zum Laufen gebracht. Nun gebe ich ungern auf. Das Thema schien mir zu zukunftsträchtig, sodass es mir keine Ruhe gelassen hat. Im nächsten Schritt kaufte ich einen 3D-Drucker inklusive Software für 10.000 Euro. Mein Drucker trug die Gerätenummer 001. Tatsächlich nutzte mich der Hersteller als Beta-Tester. Erst nachdem ich ihn vollständig auseinandergenommen und wieder zusammengebaut hatte, funktionierte der Drucker. Übrigens habe ich diesen Gerätetyp als Einziger ans Laufen gebracht. Über die Jahre habe ich mich so in die Materie eingegraben, dass ich inzwischen als ein gefragter Speaker auf Kongressen oder in Kliniken wie der OTWorld 2018 oder zuletzt der Berufsgenossenschaftlichen Unfallklinik Frankfurt am Main bin.
OT: Was fasziniert Sie an den digitalen Techniken?
Jaeger: In den Jahrzehnten meiner Tätigkeit als Orthopädieschuhmacher bin ich immer wieder an meine Grenzen gekommen. Es gab so manchen Fall für den ich keine Versorgung mit Maßschuhen oder Orthesen anfertigen konnte. Mithilfe der additiven Herstellungsverfahren gelingt es uns, in unserem Betrieb inzwischen Versorgungen mit Orthesen oder Maßschuhen durchzuführen, bei denen ich mit den traditionellen handwerklichen Methoden regelmäßig gescheitert bin. Die Erfolgsquote liegt bei uns heute, trotz der Komplexität der Versorgungen, bei annähernd 100 Prozent! Ganz ehrlich, ich fertige keinen einzigen Leisten mehr aus Holz oder Schaum. 3D-Scans und ‑Druck sindin diesem Bereich viel genauer, verbessern an vielen Stellen auch beim Orthesenbau die Passform. Die Patienten gehen etwa mit ihrem neuen Maßschuh einfach los und brauchen keinerlei Nacharbeit mehr. Das sind beglückende Momente für mich und meine Mitarbeiter ebenso wie für unsere Kunden. Dennoch: Additive Herstellungsverfahren sind kein Ersatz für das Handwerk, aber eine hervorragende Erweiterung.
OT: Lohnt sich die Anschaffung von eigenen Maschinen für additive Herstellungsverfahren für Werkstätten oder ist das eher ein Thema für die Industrie?
Jaeger: Das muss jeder für sich entscheiden. Für mich ist mein Weg klar: Ich werde, so weit, wie ich schon gekommen bin, mit eigenem Scanner und mit immer besser werdenden CAD-Kenntnissen mein eigenes Ding machen und nur dort auf die Industrie zurückgreifen, wo es sich absolut nicht vermeiden lässt. Vorteil an meiner Vorgehensweise ist die völlige gestalterische Freiheit, was das Design und die Auswahl an Materialien angeht. Die Industrie muss immer – auch bei dieser Technik – Baukastensysteme anbieten und wer einmal die Freiheit genossen hat, selbst Herr des Prozesses zu sein, will diese auch nicht mehr aufgeben. Außerdem lässt sich die Industrie diese Dienstleistung teils fürstlich bezahlen und dieser Deckungsbeitrag ist dann für den Betrieb verloren. Es besteht nach meiner Meinung auch die Gefahr, dass die Industrie durch diese Technik schon bald versucht, eigene Geschäftskonzepte am Markt zu installieren und dann kann es schnell passieren, dass der Techniker vor Ort das Nachsehen hat.
OT: Wie ist das aktuell bei Ihnen? Drucken Sie Hilfsmittel im eigenen Betrieb aus oder lassen Sie bei Partnern drucken?
Jaeger: Im Bereich Fused Deposition Modeling, kurz FDMVerfahren genannt, nutzen wir unseren eigenen Drucker für Probeschuhe und Leistenbau. Orthesen lassen wir auftrags- und materialbezogen extern bei verschiedenen Druckerdienstleistern in Deutschland drucken. Für meine Versorgungsfälle kommen drei verschiedene Materialien und damit drei verschiedene Drucker infrage. Der einfachste kostet 5.000 Euro, den habe ich bei uns in der Werkstatt stehen. Die anderen beiden Druckertypen liegen bei 100.000 Euro bzw. 300.000 Euro Anschaffungskosten. Das sind Summen, die jenseits der Wirtschaftlichkeit für einen orthopädieschuhtechnischen oder orthopädietechnischen Betrieb liegen, zumal wir die Maschinen niemals auslasten könnten. Druckdienstleister nehmen je nach Anforderung und Material zwischen 30 und 300 Euro pro Versorgung. Dieses Preis- / Leistungsverhältnis ist realisierbar für meinen Betrieb. Aber auch in der Zusammenarbeit mit diesen Dienstleistern gab es eine lange Lernkurve. Inzwischen verfügen wir aber über ein Netzwerk verlässlicher, schneller und bezahlbarer
Druckdienstleister.
OT: Können Sie uns ein paar Beispiele für „unmögliche“ Versorgungen nennen?
Jaeger: Gerne. Zwei Beispiele fallen mir spontan ein: Eine 50-jährige Patientin von uns mit einem inoperablen Pes equinovarus links, weigerte sich, unseren Maßschuh zu tragen. Zugegeben, der war optisch jenseits von Gut und Böse. Mithilfe von 3D-gedruckten Orthesen und zugerichteten Schuhen konnten wir ihr hier eine optisch akzeptablere Lösung anbieten. Eine junge Rheumatikerin haben wir mit einer Handlagerungsschiene versorgt, die wir als Ringorthese ausgeführt haben. Diese Orthese ähnelt eher einem Schmuckstück, sodass die Patientin sie mit Stolz in der Schule trägt. Tatsächlich diente mir der Armschmuck von Cleopatra, den ich in einem Film gesehen hatte, als Inspiration.
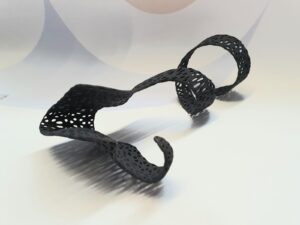
OT: Sie haben auf dem Gebiet der Orthesen bereits mit der berühmten Bauhaus-Universität Weimar zusammengearbeitet. Wie kam es dazu?
Jaeger: Mitte des Jahres 2016 habe ich bei dem Produkt-Designer und Spezialisten für Computational Design, Henning Seide, eine Schulung zur Rhinoceros-Software, einer Software für die computergestützte 3D-Modellierung und das rechnergestützte Konstruieren, gemacht. Danach war uns klar, dass wir unbedingt etwas zusammen machen müssen. Von da an haben wir angefangen, gemeinsam einzelne Produkte zu entwickeln. Bis Ende des Jahres 2016 konnten so schon verschiedene Kunden mit 3D-gedruckten Orthesen versorgt werden. Dabei haben wir sowohl das Thema Messen, als auch das Thema Design und Parametrisierung, das heißt frei wählbare Schnitte und Lochungen bearbeitet und diese drucken lassen. Mit anderen Worten, wir verfügten schon damals über einen Erfahrungsschatz mit der Durchführung von echten Kundenversorgungen – und zwar mit extrem positiven Ergebnissen. Die Passform der Orthesen war so gut, dass wir völlig auf Polsterungen verzichten konnten, was zu extrem dünnen und stabilen Versorgungen führte. Damals benutzten wir Voronoi-Lochungen die dem bionischen Prinzip von geringem Gewicht bei höchster Stabilität folgten. Selbst mit dem Drucken von thermoplastischem Polyurethan (TPU)-Materialien hatten wir schon erste Erfahrungen gesammelt, als sich Prof. Andreas Mühlenberend und Prof. Jan Willmann von der Bauhaus Universität Weimar an Henning Seide, Absolvent des Studiengangs Produktdesign der Bauhaus Universität Weimar, zwecks einer Machbarkeitsstudie von Orthesen im additiven Herstellungsverfahren wandte. Als einer der wenigen, die in der Zeit schon echte Patientenversorgung auf dem Gebiet durchgeführt hatten, gehörte ich schnell zum Team dazu. Mit dabei war auch der Designer und ebenfalls Absolvent der Bauhaus Universität, Niklas Hamann.
OT: Was war die Aufgabenstellung an Ihr Unternehmen?
Jaeger: Die Universitäten sind heute für viele Forschungsprojekte auf das Einwerben von Forschungsgeldern bei Partnern angewiesen. Das galt auch für unser gemeinsames Projekt, sodass mein Betrieb im Forschungsantrag als sogenannter „Industriepartner“ für die Machbarkeitsstudie angegeben war. Wir sollten unsere Ideen für die Patientenversorgung mit additiv hergestellten Produkten einbringen und die Praxistests übernehmen.
OT: Wie sah die Zusammenarbeit im Detail aus?
Jaeger: Da ich Handwerker bin, habe ich als Erstes klassisch eine Orthese gebaut. Diese war dann Ausgangspunkt für die weitere Zusammenarbeit mit den Weimarern. Im Ergebnis entstand die „Total Zoning Orthese“ – eine Begriffsschöpfung von Professor Mühlenberend. Dieser Begriff überschreibt die Idee, die wir 2017 zu Beginn der Machbarkeitsstudie gemeinsam entwickelt haben, nämlich eine Orthese völlig digital zu messen, zu modellieren und zu fertigen. Dabei ist die Gestaltung und der Schnitt durch das modellieren im CAD völlig frei und ist alleine durch die versorgungstechnischen Notwendigkeiten und die Vorstellungskraft des Versorgenden vorgegeben, heißt, im Grunde ist jede Orthese ein Einzelstück, wie ja auch in der klassischen Versorgung durch den Orthopädietechniker
OT: Wie beurteilen Sie das Ergebnis der Kooperation im Rückblick?
Jaeger: Ich habe viel gelernt, vor allem was die Zusammenarbeit mit einer Universität angeht. Leider ging die Zusammenarbeit dann nicht über die Machbarkeitsstudie hinaus, weil die Anträge auf weitere Forschungsgelder trotz mehrfacher Versuche nicht bewilligt wurden, so dass das Projekt derzeit in einer Warteschleife hängt.
OT: Bieten Sie diese Orthesen auch Ihren Kunden an?
Jaeger: Ja. Henning Seide und ich haben, nachdem sich die Genehmigungsphase für die weiterführende Forschung hinzog, weiter Kunden versorgt und haben dabei spektakuläre Erfolge erzielt. Unsere Entwürfe sind bei Weitem nicht so experimentell und minimal wie die mit der Bauhaus Universität Weimar, aber in der Form genauso wie unsere Patienten es benötigen, um besser laufen zu können.
OT: Wagen Sie zum Abschluss des Gesprächs eine Prognose zur Zukunft des 3D-Drucks in der Orthopädie-Technik?
Jaeger: Für mich steht fest, dass diese Technik unsere Branche in kürzester Zeit revolutionieren wird.
Die Fragen stellte Ruth Justen.
- Dirk Treiber findet bei Enovis neue berufliche Heimat — 13. August 2025
- Rehavision – Netzwerken und Nachwuchs fördern — 2. Juli 2025
- Das Handwerk trauert um Werner Dierolf — 28. September 2024