Am Ende der digitalen Prozesskette steht der Druck. Doch diesem gehen wichtige Schritte voraus. Welche Rolle spielt der Scan für das Endprodukt?
Axel Ruppert: Eine riesige Rolle. Digitale Technik funktioniert nach dem Prinzip „Shit in, shit out“. Wenn ich vorne etwas Schlechtes hineingebe, kann ich nicht erwarten, dass hinten etwas Gutes herauskommt.
Was zeichnet Ihrer Meinung nach einen perfekten Scan aus?
Wenn er die Oberfläche so erfasst, dass für den nachfolgenden Produktionsschritt alles Notwendige daraus hervorgeht.
Mit jedem Teil ihres Werkzeugkastens sind Techniker bestens vertraut. Scanner waren jedoch lange kein klassischer Bestandteil. Kann man diese Technik ganz einfach integrieren?
Grundsätzlich ja, aber es braucht ein Verständnis dafür. Es ist wichtig, sich darüber klar zu werden, wie Scanner arbeiten und wie ein Scankörper entsteht. Es ist – wie viele denken – kein Foto, sondern eine Stück für Stück entstehende Punktwolke. Der Scanner erfasst also einzelne Kontaktpunkte. Er sendet zum Beispiel Infrarot-Licht zum zu scannenden Objekt und erhält eine Reflexion zurück. Diese Reflexion registriert er als einen bestimmten Punkt. In der Nähe gibt es dann die nächste Reflektion und die nächste und nächste. Über diese Sammlung von Reflexionspunkten entsteht letztendlich die Punktwolke. Wenn man das verstanden hat, tut man sich bei der Arbeit wesentlich leichter.
Wie finde ich heraus, welcher Scanner zu meinem Betrieb passt?
Es ist wichtig, dass man sich überlegt, was man scannen will. Ist es zum Beispiel ein „totes“ Anbauteil für einen Rollstuhl, also eine geometrische Form, brauche ich gegebenenfalls eine andere Scantechnik, als wenn ich einen lebendigen Körper, also eine anatomische, runde Form vor mir habe, an der sich der Scanner während des Scanprozesses nicht gut „festhalten“ (das sog. Tracking) kann. Es macht auch einen Unterschied, ob ich einen Erwachsenen vor mir habe, der stillhalten kann, oder ein Kind, das sich bewegt. Im zweiten Fall brauche ich einen Scanner, der sich extrem gut am Objekt „festhält“ und dazu am besten zusätzlich auf dem Objekt angebrachte Markerpunkte nutzt. Diese Reflexionspunkte geben dem Scanner eine Orientierung – er erkennt zum Beispiel, wenn sich das Objekt dreht, und kann die nächste erfasste Fläche trotzdem sicher der Form zuordnen.
Für Einsteiger ist es zudem hilfreich, wenn man den Scanvorgang pausieren kann. Stellt man fest, dass man eine Stelle übersehen hat, kann man einfach wieder einsteigen und den Scan komplettieren.
Es gibt verschiedene Dateiformate, in denen ein 3D-Modell zur Verfügung gestellt werden kann. Die beiden gängigen sind OBJ und STL. Welches sich am besten anbietet, hängt davon ab, was man scannen will. Das STL-Format beschreibt nur die Oberflächengeometrie eines Objekts, das OBJ-Format enthält zusätzlich die Textur, also quasi das Oberflächenfoto. Wenn man keine prominenten Stellen wie erhabene Knöchel oder Zehnenballen markieren muss, reicht das STL-Format aus. Arbeitet man aber mit Anzeichnungen bei der Konstruktion, ist das OBJ-Format die bessere Wahl.
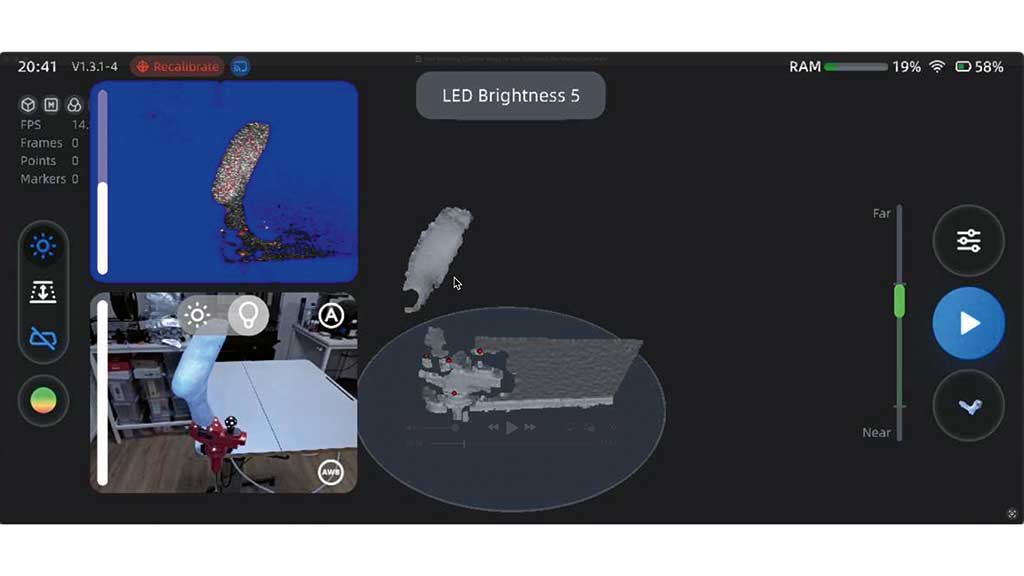
Gibt es weitere Punkte, die Betriebe beachten sollten?
Auf jeden Fall die Auflösung des Scans. Welchen Anspruch habe ich? Wie genau muss der Scan sein? Man könnte denken: Je höher die Auflösung, desto besser das Ergebnis. Das stimmt aber so nicht. Es kommt immer darauf an, was ich scannen und später damit machen will. Brauche ich viele Details, benötige ich auch eine hohe Scan-Auflösung. Geht es nicht um Details, kann zu viel Genauigkeit dagegen zu unnötig großen Scan-Dateien führen. Aus meiner Sicht wurde hier früher in unserer Branche etwas übertrieben – da sprach man von notwendigen Auflösungen von 0,5 Millimetern. Wenn man sich im Bereich um 1,5 Millimeter bewegt, fährt man meiner Meinung nach heute ganz gut.
Für Einsteiger bietet zum Beispiel die Firma Shining eine hilfreiche Funktion an: die „Datenqualitätsanalyse“. Die Punktwolke entsteht zu Beginn des Scans in der Farbe Rot und wechselt dann zu Grün, wenn die gesamte Fläche sicher erfasst wurde.
Betriebe sollten auch den Einsatzort berücksichtigen. Wer nicht vor Ort scannt, benötigt maximale Mobilität. Dafür eignen sich schnurlose all-in-one-Geräte. Will ich mobil arbeiten, dann lande ich momentan unweigerlich beim Modell „Einstar Vega“ von der Firma Shining oder bei den „Miraco“-Scannern von Revopoint.
Besonders beim Einsatz schnurgebundener Scanner muss man die Systemvoraussetzungen für den angeschlossenen Laptop/PC beachten. Denn die Software, mit der ich den Scan erstelle bzw. nachbearbeiten will, muss darauf schließlich auch sauber laufen. Gut bedient ist man wegen der hohen Grafikleistung oft schon mit einem Gerät, das für Gamer ausgelegt ist, und man packt sicherheitshalber zusätzlichen Arbeitsspeicher drauf. Eine „Nvidia“-Grafikkarte – das ist „State of the Art“ – mit 32 Gigabyte Speicher und einem Arbeitsspeicher von 64 Gigabyte verhindert Verdruss bei den Mitarbeitenden und sichert ein flüssiges Arbeiten im 3D-Bereich. Man kann einem Mitarbeiter keinen einfachen Rechner aus der Werkstatt an die Hand geben, auf dem sonst die Abrechnungssoftware läuft und dann am besten auch noch alles auf demselben Laufwerk ablegen. Man sollte von Beginn an eine Ablagestrategie für die Scandaten festlegen und auch Archivierungsfristen definieren – dabei gilt es, immer den Datenschutz zu beachten.
Wer unterwegs im Einsatz ist, muss auch die Möglichkeit haben, die Daten schnell und einfach zu übertragen. Shining bietet eine Cloud an, in der die Daten direkt vom Scanner abgelegt und mit Kollegen an anderen Standorten geteilt werden können.
Privat ist das Handy für mehr und mehr Dinge im Einsatz. Auch Scannen ist per Handy und Tablet möglich. Mit welchen Geräten haben Sie gute Erfahrungen gemacht?
Sehr bekannt in der Branche ist der „Structure Sensor“, der auf das iPad gesteckt wird und daraus einen vollwertigen 3D-Scanner macht. Das hört sich erst einmal gut an, doch es gibt auch Schattenseiten. Apple hatte zum Beispiel Ende 2023 aufgrund von Sicherheitsbelangen in kurzer Folge ein Update nach dem anderen herausrausgegeben. Die Versionssprünge hatten negative Auswirkungen auf die Scanqualität und verschlechterten die Kommunikation zwischen Sensor, Betriebssystem und Scan-App. Weit verbreitet sind die iOS Scan-App „3DSizeMe“ von Qwadra und die PC-Nachbearbeitungssoftware „MSoft“, die beide speziell für die Orthopädie-Technik ausgelegt sind. Im Gegensatz zu anderen Scan-Lösungen sind diese Tools für das Scannen des menschlichen Körpers optimiert. Auch das anatomisch korrekte Schließen von Löchern im Scan funktioniert hier besonders gut. Das macht die Nachbearbeitung deutlich einfacher. Die Firma bietet zur Nutzung ein spannendes Lizenzmodell an. Die Scan-App steht kostenlos im App-Store zur Verfügung. Auch die PC-Software ist kostenlos zu haben. Erst beim Speichern der Daten im STL- oder OBJ-Format fallen Kosten an. Durch das Pay-per-use-Modell handelt es sich also nicht um eine permanent laufende Lizenz. Das ist gerade zum Start von Vorteil, wenn man noch gar nicht weiß, wie oft man damit tatsächlich scannen will. Damit geht man quasi kein Risiko ein.
Derzeit begeistert mich die iOS Springer-3D-Scan-App von Springer Aktiv, die auf der Basis der App Snugfit mit einem iPhone/iPad Pro funktioniert. Das Besondere: Es ist kein Aufstecksensor erforderlich. Geräte ab dem iPhone 11 Pro oder iPad Pro haben den notwendigen Sensor über ihre Face-ID-Funktion bereits integriert. Die App macht wirklich einen guten Job und läuft ebenfalls im Pay-per-use Modell. Und die Entwicklung geht weiter. Snugfit arbeitet derzeit an einer Software, die aus einer einfachen Videoaufnahme eine 3D-Datei generiert. Ich glaube, künftig geht die Technik genau dorthin. Auch Antonius Köster präsentierte auf der 3D-Druck-Messe Formnext in Frankfurt eine Software, die aus einem Video eine perfekte 3D-Datei generieren kann.
Wie nimmt man die Mitarbeiter auf dem Weg mit? Wie etabliert man den digitalen Workflow?
Wenn man nicht von Anfang an Acht gibt, kann es passieren, dass man sich verspielt und unnötige „Kreativität“ in Prozesse hineinsteckt, die viel Zeit fressen, aber ins Leere laufen. Es müssen Standards definiert werden. Mit Blick auf die strategische, zentrale Datenablage sind insbesondere die Führungsebene sowie die technische Führungsebene in der Werkstatt gefragt. Man kann den Mitarbeitern nicht einfach einen Scanner in die Hand drücken und sie loslaufen lassen.
Gerade wenn man Neues lernt, kann Ausprobieren auch ein wichtiger Teil des Lernprozesses sein, oder?
Definitiv, aber wir sind ja nicht mehr in der Phase, in der wir graue Flecken auf der Landkarte erkunden, von denen wir noch nichts wissen. Wir müssen das Rad nicht neu erfinden. Es gibt mittlerweile Erfahrungswerte, es gibt genügend Experten, die sich mit dem Thema beschäftigen. Wenn man sich noch außerhalb dieser Informationsblase befindet, muss man sich eben hineinbegeben.
Nicht nur für große Betriebe kann es günstiger sein, für einen Tag einen Experten ins Haus zu holen, mit dem dann gemeinsam ein Prozess aufgesetzt wird. Sollen nicht nur ein Mitarbeiter, sondern mehrere mit der Technik arbeiten, lohnt es sich auch, hierfür einen Schulungstag anzubieten. Dann können Testscans von verschiedenen Versorgungen durchprobiert und auch die Nachbearbeitung oder der Versand der Daten an Fertigungspartner durchgespielt werden.
Wie klappt aus Ihrer Sicht der Start in die digitale Welt der 3D-Fertigung am besten?
Von der Führungsebene braucht es eine Vision, eine Strategie, die ins Team getragen wird. Gute Erfahrungen mache ich dort, wo eine verantwortliche technische Führungskraft benannt ist und auf Arbeitsebene interessierte Mitarbeitende von Beginn an eingebunden werden. Dann kann es nur gut werden und es macht auch allen Beteiligten Spaß. Und wenn es Spaß macht, wird die Sache zum Selbstläufer. Ich kann nur raten: Setzt früh eure jungen Kräfte ein, die motiviert sind, sich mit neuen digitalen Themen auseinanderzusetzen, und signalisiert ihnen, dass die Verantwortung künftig bei ihnen liegen wird. Fordert und fördert sie!
Es werden sich auch ganz neue Arbeitsabläufe ergeben, wenn man sich die Frage stellt: Welche Kraft mit welcher Kompetenz setze ich wie lange für welchen Arbeitsschritt ein? Mit einem abgestuften Rechtesystem können auch Azubis schon früh in die digitale Fertigung eingebunden werden – die Kontrolle und Bestellung selbst übernimmt dann anschließend die Führungskraft. Es gibt Systeme, wie beispielsweise das proprio AFO-Konzept von Springer Aktiv, die solche Abläufe ermöglichen.
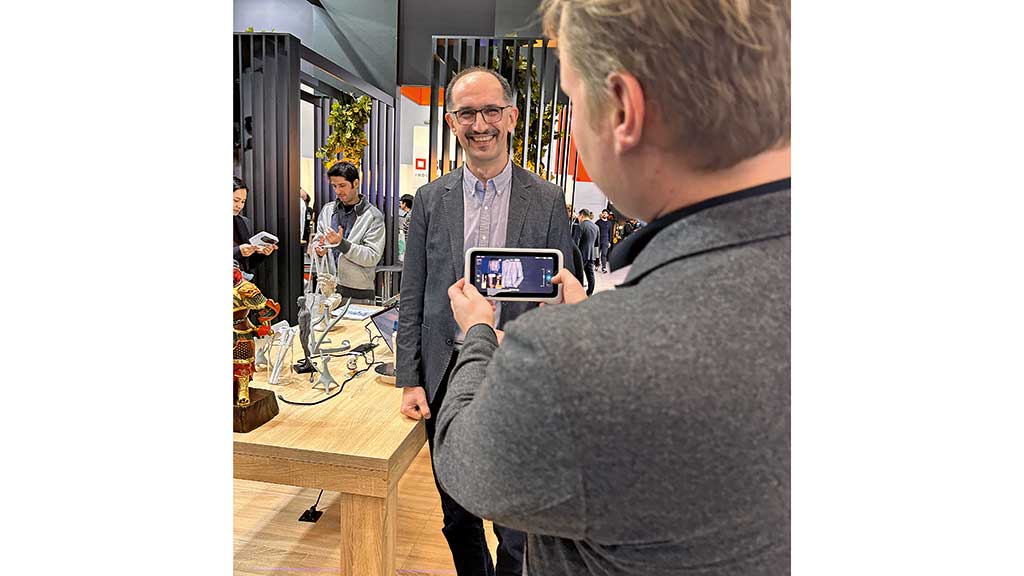
In welche Bereiche muss das Team während der Implementierung noch eingebunden werden?
Ganz wichtig ist es, frühzeitig für die Dateiablage eine Verzeichnisstruktur und eine klare, abteilungsübergreifende Dateibezeichnung für die Scans zu definieren. Nur so wird ein Wiederauffinden sichergestellt und man kann später auch effizient aufräumen – nach zehn Jahren zum Beispiel sagen: „Lösche alle Dateien mit der Endung XX von 2014.“ Aber solche Prozesse sollte man auch im QM-System festlegen. Außerdem braucht es auch eine Datenschutzstrategie – schließlich reden wir hier über sensible digitale Daten.
Gibt es typische Anfängerfehler?
Ein Klassiker ist es zum Beispiel, beim Scannen zu nah an das Objekt zu gehen. Der Mensch neigt einfach dazu, wenn etwas genau werden soll, näher heranzugehen. Beim 3D-Scan brauche ich aber einen gewissen Abstand. Die meisten Scanner zeigen an, ob es passt oder nicht, und wenn man sich daran orientiert, dann funktioniert die Erfassung auch sauber.
Mich auf den Arbeitsabstand des Scanners einzulassen, kann auch bedeuten, dass ich meine Umgebung anpassen muss. Ich brauche Bewegungsfreiheit rund um den Patienten. So habe ich dann einen ausreichend großen Radius, in dem ich den Scanner um den Patienten herumführen kann. Ein mitten im Raum freistehender Schraubstock eignet sich besser, um ein Gipsmodell zu scannen, als ein an der Werkbank montierter. Das sind Kleinigkeiten, mit denen ich mir im Alltag aber Probleme ersparen kann.
Müssen bei der Arbeitsumgebung weitere Faktoren berücksichtigt werden?
Ja, ich brauche eine gute Raumausleuchtung oder ein Licht am Scanner, um eine gleichmäßige Oberflächentextur zu erhalten. Auch der Einsatz eines Structure Sensors, der mit Infrarot-Detektion arbeitet, und pralle Sonne im Raum funktionieren zum Beispiel nicht zusammen. Weißlichtscanner dagegen sind lichtunempfindlicher. Aus diesem Grund kombinieren mittlerweile Scanner, wie zum Beispiel der Einstar Vega von Shining, mehrere Scan-Technologien. Die doppelte Erfassung führt zu sichereren Scanergebnissen.
Gibt es noch andere Tipps oder Kniffe, die Sie Anfängern mit auf den Weg geben möchten?
Schwarze Gegenstände, ein Klarsichtschaft oder reflektierende Gegenstände kann ich nicht einscannen – da die Reflektion gestört oder unmöglich ist. Wenn Prothetiker einen Testschaft scannen wollen, gibt es die Möglichkeit, sogenannte Tanning-Sprays einzusetzen. Dank des Sprays wird die Oberfläche für eine gewisse Zeit weiß. Die Farbe verschwindet anschließend aber von allein rückstandslos.
So simpel es klingt: sich informieren und austauschen. Das Wissen ist vorhanden. Holt euch jemanden ins Haus, der euch berät, oder fragt Kollegen nach Empfehlungen. Jeder sammelt eigene Erfahrungen, von denen man gegenseitig profitieren kann. Es gibt nicht die eine Lösung. Es gibt mittlerweile zahlreiche Lösungen. Wir müssen uns aber im Klaren darüber sein, dass diese nicht alle für die Orthopädie-Technik ausgelegt sind. Autoteile zum Beispiel haben Ecken und Kanten – die sind „einfach“ zu scannen im Gegensatz zu anatomischen, runden Formen in der Orthopädie-Technik.
Was ich jedem ans Herz legen kann: Besucht die Formnext in Frankfurt. Die Messe ist inzwischen absolut in der Branche etabliert. Und sei es nur, um die Scheuklappen ein wenig zu öffnen und einfach mal zu schauen, welche Neuerungen es gibt. Es lohnt sich, Mitarbeitern, die regelmäßig scannen und drucken, einen Einblick in diese Welt zu ermöglichen.
Um beim Blick in die Zukunft zu bleiben: Sehen Sie weitere Entwicklungen kommen?
Aus einer Videoaufnahme eine 3D-Datei zu generieren, ist – wie gesagt – bereits möglich. Dabei muss das Objekt aber ein unbewegliches Modell oder ein Körper sein, der stillhält. Die nächste Stufe wäre es, ein bewegtes Modell aufnehmen zu können. Pendelt beispielsweise ein Fuß beim Sitzen auf der Liege hin und her oder wird verdreht, wird es dann kein Problem mehr sein, daraus eine 3D-Datei zu erzeugen. KI wird uns hierbei neue Möglichkeiten eröffnen, wo wir heute noch vor Herausforderungen stehen.
Die Fragen stellte Pia Engelbrecht.
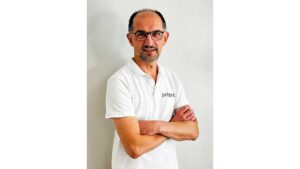
Axel Ruppert ist Orthopädieschuhmacher- und Orthopädietechnik-Meister sowie staatlich geprüfter Podologe. 35 Jahre lang war er Inhaber des Vital-Zentrums Ruppert in Schlüchtern, bevor er das Unternehmen 2021 an die Sanitätshaus Kaphingst-Gruppe übergab. 1992 gründete er die Beratungsfirma Ruppert GmbH, die sich heute auf die Unterstützung bei der Einführung digitaler Konstruktions- und Fertigungsprozesse spezialisiert hat. Er betreut außerdem für die Springer Aktiv AG als Technischer Key-Account das „proprio AFO Konzept“ mit 3D-gedruckten, pädiatrischen Orthesen in der praktischen Umsetzung bei Betrieben vor Ort.
Hier finden Sie alle 6 Artikel unserer neuen Serie „Additive Fertigung – Teil 1: Scannen“:
- Der Weg in die Additive Fertigung
- 3D-Scanner im Überblick
- Praxisbeispiel zur additiv gefertigten Einlagenversorgung
- Praxisbeispiel zur additiv gefertigten Sitzschalenversorgung
- Per Korrekturgestell zum individuellen Korsett
- Mit Punktwolke zur Präzision
- Rehakind bündelt wissenschaftliche Evidenz — 5. September 2025
- Kleines Jubiläum für KIM — 4. September 2025
- OTWorld nimmt Orthopädie-Schuhtechnik in den Fokus — 3. September 2025