Polyamid ist aus der Textilindustrie nicht mehr wegzudenken. Auch bei der Herstellung von Kompressionsware überzeugt das Material durch seine Eigenschaften. Doch für die Umwelt stellt der gängige Hauptrohstoff zur Erstellung der Fasern eine Belastung dar. Auf eine Alternative setzt der Medizinproduktehersteller Ofa. Statt Erdöl kommen alte Reifen zum Einsatz. Wie das funktioniert und welchen Einfluss diese „Ressource“ auf die Produkte hat, verrät Produktmanagerin Jennifer Hornung im Gespräch mit der OT-Redaktion.
Unternehmen gehen verschiedene Wege, um ihren ökologischen Fußabdruck zu verringern. Ofa setzt unter anderem beim Material an. Wie viel Potenzial steckt in diesem Bereich?
Jennifer Hornung: Wir sehen darin enormes Potenzial, denn Kompressionsstrümpfe bestehen häufig zu mehr als 50 Prozent aus Polyamid – hergestellt aus der endlichen Ressource Erdöl. Mit der Nutzung von nachhaltigerem Polyamid können wir und die gesamte Industrie einiges bewirken, denn neben den positiven Auswirkungen auf unsere Umwelt machen wir uns gleichzeitig unabhängiger von einem endlichen Rohstoff.
Polyamid gilt als Standard für die Herstellung von Kompressionsware. Gibt es denkbare Alternativen?
Mit herausragenden Eigenschaften in Festigkeit, Formbeständigkeit und Elastizität sowie Hautverträglichkeit und Haltbarkeit ist Polyamid derzeit ein unverzichtbares Material in der Produktion von medizinisch wirksamer Kompression. Die beste Alternative aus unserer Sicht ist deshalb ein nachhaltigeres Herstellungsverfahren.
Polyamid wird vorwiegend aus Erdöl hergestellt. Sie setzen auf Altreifen. Warum fiel die Wahl ausgerechnet auf dieses Material?
Zugegeben, die Kombination Reifen und Strümpfe klingt erst einmal ausgefallen. Es gibt allerdings eine innovative und technisch ausgereifte Lösung, um aus Altreifen sogenanntes Pyrolyseöl zu gewinnen. Dieses kann bei der Herstellung von Polyamid große Teile des sonst notwendigen Rohöls ersetzen. Da wir wissen, dass für viele Kunden Nachhaltigkeit noch nicht das Kaufkriterium Nummer eins ist, haben wir uns dazu entschlossen, nicht eine weitere nachhaltige Alternative auf den Markt zu bringen, sondern ein etabliertes und beliebtes Produkt – unsere elegante medizinische Kompression „Memory“ – mit diesem nachhaltigeren Polyamid weiterzuentwickeln.
Beschreiben Sie bitte kurz den Recyclingprozess.
Für die Herstellung unseres Garns wird das sogenannte Pyrolyseverfahren genutzt. Dabei werden die Kohlenstoffketten in den Reifen in einem thermochemischen Prozess auf molekularer Ebene zerlegt und chemisch umgewandelt. Das daraus gewonnene Pyrolyseöl wird dann in die Polyamid-Herstellung integriert und kann große Teile des sonst benötigten Rohöls ersetzen. Der nachhaltigere Rohstoff wird unserem zertifizierten Polyamid über den sogenannten Massenbilanzansatz zugerechnet, was im Produktionsprozess letztendlich CO2-Emissionen einspart.
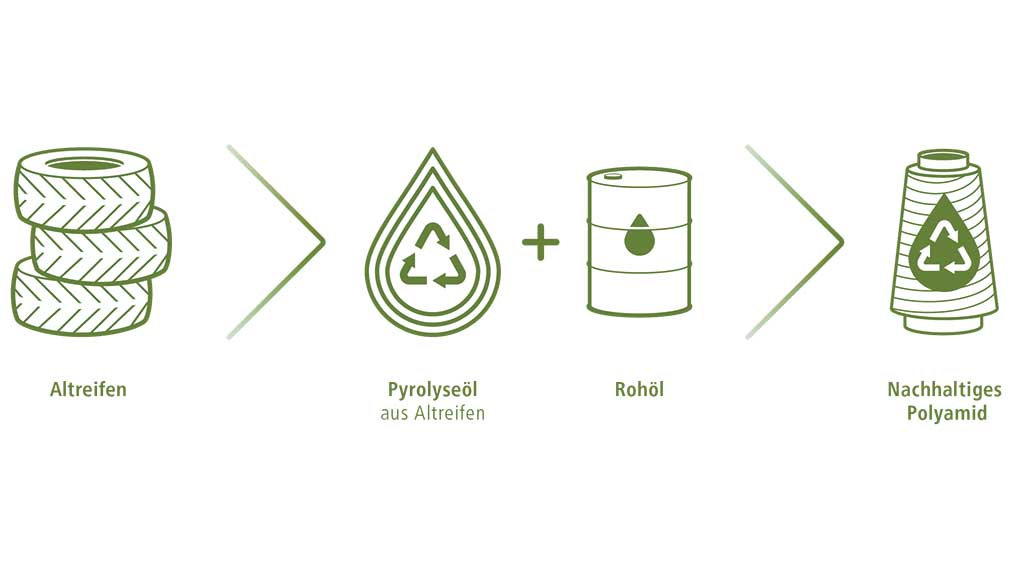
Inwiefern genau verringert sich durch dieses Verfahren der ökologische Fußabdruck?
Wir können die Emissionsreduktionen durch eine Analyse des gesamten Lebenszyklus des Materials ermitteln. Das nachhaltigere Ausgangsmaterial von BASF verfügt über eine zertifizierte Umweltbilanz. Diese Bilanz, die nach den Standards der ISO 14040/44 erstellt und von unabhängigen Fachleuten überprüft wurde, zeigt eine CO2-Einsparung von etwa 67 Prozent im Vergleich zur Herstellung von herkömmlichem Polyamid-Garn. Zusätzlich recyceln wir durch die Verwertung von Altreifen ein Material, das schwer recycelbar ist. Das bedeutet, wir tragen nicht nur zur Reduzierung von Emissionen bei, sondern helfen auch, Abfall zu minimieren und Ressourcen zu schonen.
Welcher Prozessschritt ist besonders herausfordernd?
Der Pyrolyseprozess, den einer unserer Vorlieferanten durchführt, ist technisch sehr anspruchsvoll. Für uns bei Ofa liegt die eigentliche Herausforderung jedoch in einem anderen Bereich. Medizinische Hilfsmittel unterliegen strengen Regulatorien und Normen. Das bedeutet, dass wir nicht nur den komplexen Prozess der Garnherstellung berücksichtigen müssen, sondern auch sicherstellen müssen, dass unsere Produkte trotz des Einsatzes neuer Garne mit einem Anteil von recyceltem Material alle Qualitäts- und Sicherheitsstandards gemäß RAL (Deutsches Institut für Gütesicherung und Kennzeichnung, Anm. der Red.) und MDR (Medical Device Regulation, Anm. der Red.) erfüllen. Um dies zu gewährleisten, haben wir umfangreiche Tests und Prüfverfahren implementiert. Unsere Produkte durchlaufen strenge Qualitätskontrollen intern sowie extern. So stellen wir sicher, dass unsere medizinischen Hilfsmittel nicht nur nachhaltig, sondern auch sicher und zuverlässig sind.
Gibt es Unterschiede im Aussehen, Tragegefühl oder in der Funktionalität zwischen Kompressionsware aus herkömmlichem Polyamid und solcher aus recycelten Reifen?
Nein, hier gibt es absolut keine Unterschiede. Wir haben intensiv daran gearbeitet, sicherzustellen, dass unsere neue Kompression dieselben hohen Standards erfüllt. Unsere Kunden erhalten den Komfort und die Qualität, Optik und Haptik, die sie gewöhnt sind – nur eben nachhaltiger.
Sie sagten, dass bei vielen Kunden Nachhaltigkeit nicht das Kaufkriterium Nummer eins ist. Spielt das Thema bei der Entscheidung dennoch eine Rolle?
Solange Preis, Optik und Komfort stimmen, ist Nachhaltigkeit für einen wachsenden Anteil an Kunden und Patienten ein entscheidendes Kriterium. Der nachhaltige Erfolg unserer Bemühungen hängt von der Akzeptanz unserer Produkte ab, denn Investitionen in Innovationen lohnen sich nur dann, wenn die Produkte auch angenommen werden. Außerdem gibt es bereits Bestrebungen von Krankenkassen, Nachhaltigkeit als Faktor für Erstattungspreise und die Zulassung von Hilfsmitteln zu etablieren. Das wiederum würde auch die Kaufentscheidung von Kliniken, Krankenhäusern, Großhändlern und Verbänden beeinflussen.
Die Fragen stellte Pia Engelbrecht.
- Sanitätshaus im Einsatz beim „Wacken Open Air“ — 29. August 2025
- Nachholbedarf in Sachen Digitalisierung — 28. August 2025
- Ottobock übernimmt Romedis — 27. August 2025