Um insbesondere kleineren und mittleren Betrieben mehr Sicherheit und Effizienz im Umgang mit der additiven Fertigung inklusive der technischen und rechtlichen Hintergründe zu bieten, starteten im März 2020 verschiedene Akteure aus Industrie, Forschung und Lehre sowie Dienstleistungsunternehmen der Gesundheitsbranche (siehe Abbildung 2) das auf drei Jahre angelegte Verbundprojekt „SIGMA3D – Simulationsgestützte Medizintechnikplattform zur individuellen 3D-Hilfsmittelversorgung“.
Entwicklung einer Plattform bis 2023
Das Gesamtziel des Verbundprojekts SIGMA3D ist die interdisziplinäre Konzeption, Entwicklung und exemplarische Umsetzung einer digitalen Prozesskette zur Fertigung von orthopädischen Hilfsmitteln. Projektbestandteile sind daher alle Prozessschritte von der Erfassung und Digitalisierung des Patienten über die Konstruktion und virtuellen Prüfung des Hilfsmittels, bis zur exemplarischen Produktion mittels additiver Verfahren und erforderlichen Prozessvalidierungschritten.
Geplant ist eine Plattform, die eine neuartige Entwicklungs- und Testumgebung für die Orthopädie-Technik darstellt. Die Orthesen sollen mithilfe der Plattform auf Basis der Patientendaten (3D-Scan, Fotos etc.) patientenindividuell in 3D modelliert und simuliert werden. Erstmalig soll dabei eine automatische virtuelle Sicherheitsprüfung durch validierte Belastung- und Funktionstests auf Basis von Finite Elemente Simulationen rfolgen. Ein weiterer Fokus des Projekts ist die gezielte Optimierung der Konstruktion sowie der Gebrauchseigenschaften der Orthesen für die additive Fertigung im engen Austausch mit Anwendungspartnern.
Der angestrebte Ablauf der simulationsgestützten Hilfsmittelversorgung ist in Abbildung 1 in vereinfachter Form dargestellt. Angefangen beim Sanitätshaus mit dem Scannen des Patienten über die Auswahl und Modellierung eines geeigneten Hilfsmitteldesigns inklusive unterschiedlicher Vorschaumöglichkeiten, der Schnellprüfung der Konstruktion, bis zur Konstruktionsabnahme und ästhetischen Produktindividualisierungsmöglichkeiten. Es folgt eine vollständige Finiten-Elemente-Analyse (FEA) für eine detaillierte mechanische Untersuchung und die benötigte Dokumentation. Abschließend wird das individuelle Hilfsmittel additiv gefertigt und ausgeliefert. Aspekte, wie die Analyse und Dokumentation der regulatorischen Anforderungen, die Prozessvalidierung der Fertigungsanlagen sowie die Validierung der FEA sind ebenso Teil der Plattformentwicklung.
Arbeitsziele des Projektkonsortiums
Um die Plattform wie beschrieben zu realisieren, hat das Projektkonsortium folgende Arbeitsziele definiert:
- Konzeption verifizierbarer Scan- und Messverfahren, welche ein zur Modellerstellung geeignetes digitales Patientenmodell ermöglichen, das in der Qualität dem aktuellen Goldstandard (Gipsabformung) mindestens gleichwertig ist: Dazu sollen im Projekt neue Scanvorrichtungen konzipiert werden, die helfen sollen, den Patienten in optimaler Position zu erfassen, Korrekturen zu ermöglichen und abgestimmt mit digitalen Bibliotheken, die Scandaten in optimaler Ausrichtung zu exportieren. Zur Bewertung und Kalibrierung von neuen Scannern werden Referenzen aufgebaut und in Softwarebibliotheken hinterlegt.
- Softwaretechnische Konzeption und Umsetzung einer Web-Plattform für die Modellierung und virtuelle Prüfung von additiv zu fertigenden Hilfsmitteln (Orthesen), inklusive der erforderlichen Schnittstellen zu Drittsystemen: Die Plattform soll auf einer Microservice-Architektur basieren. Somit wird für eine hohe Flexibilität und Robustheit der Plattform bei gleichzeitig strikter Datentrennung jedes einzelnen Nutzers gesorgt. Den Patienten soll eine Hilfsmittelproduktvorschau in 3D sowie Möglichkeiten der visuellen Mitgestaltung und zum Nutzerfeedback geboten werden.
- Implementierung geeigneter Softwarekomponenten für die webbasierte Modellierung/Anpassung von auf der Plattform hinterlegten generischen Hilfsmitteldesigns.
- Erforschung von mindestens zwei und Implementierung mindestens eines Produktdesigns (Use-Case-Orthese) zur Erprobung und Validierung des angestrebten Workflows. Dazu müssen biomechanisch geeignete Materialkombinationen und Strukturen untersucht werden.
- Konzeption und Implementierung von Modellen zur automatisierten Optimierung der hinterlegten Produktdesigns und der vom Orthopädietechniker gewünschten Produktanpassungen anhand der Patientendaten. Dazu wird eine Methode entwickelt und implementiert, bei der das Modell eines Hilfsmittels eine parametrische Optimierung durchläuft und die Variablen durch mathematische Algorithmen systematisch modifiziert werden, bis eine Verbesserung des bestehenden Designs oder ein Optimum gefunden wurde. Hier gilt es die Designvariablen zu identifizieren, die den größten Einfluss auf die Optimierung haben und entsprechende Zielkriterien (Funktionalität, Sicherheit, Robustheit, Gewicht) festzulegen.
- Konzeption und Implementierung validierter Simulationsverfahren für die automatisierte, normkonforme, virtuelle Belastungs-/Sicherheitsprüfung der auf der Plattform modellierten Hilfsmittel. Ansatzpunkt ist hierbei, dass für ein Hilfsmitteldesign verschiedene Variationen per FEA geprüft werden. Innerhalb der geprüften Rahmenbedingungen können Funktionalität und Sicherheit individueller Designs gewährleistet werden und eine Produktionsfreigabe erfolgen. Um diese virtuelle Prüfung zu validieren, ist es erforderlich, dass physikalische Prüfverfahren zur Funktions- und Betriebsfestigkeitsprüfung von additiv gefertigten Orthesen entwickelt und auf im Projekt aufzubauenden Prüfständen validiert werden. Die Art und die Richtung der Belastungen sowie die Randbedingungen werden dabei definiert und können in die Simulation übernommen werden.
- Evaluierung geeigneter additiver Fertigungsmethoden und Materialien. Durch die neue MDR wird es in Zukunft notwendig sein, die Fertigungsanlagen (3D-Drucker) einer umfassenden Prozessvalidierung zu unterziehen. Auch die Software zur Steuerung des 3D-Drucks kann Merkmale aufweisen, die zu ihrer Einstufung als Medizinprodukt führen. Daher sollen die im Projekt untersuchten und erprobten Fertigungsverfahren und Materialkombinationen mit Hinblick auf die zukünftig zu erwartenden regulatorischen Anforderungen evaluiert werden.
- Untersuchung von Möglichkeiten einer (teil-)automatischen individuellen Nutzenevaluation des Hilfsmittels für die Krankenkassenerstattung auf Basis der Simulation und der Prüfberichte.
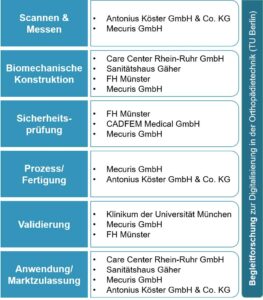
Erwartete Vorteile für OT-Betriebe und Verbundpartner
Von der angestrebten Plattform erhoffen sich die Projektpartner (Abb. 2) die Senkung der Versorgungskosten. Mithilfe der Plattform soll ebenfalls die Weiterentwicklungen von bestehenden Produkten erleichtert sowie die Produktqualität und Sicherheit verbessert werden.
Besondere Bedeutung komme aus Sicht der Partner einer solchen digitalen Plattform im Umgang mit den aktuellen und zukünftigen regulatorischen Anforderungen zu. Durch die automatische parametrische Optimierung der Produktdesigns auf Basis der Patientendaten und die im Hintergrund ablaufende Belastungsprüfung der entworfenen Hilfsmittel, werde erstmalig eine Möglichkeit geboten, patientenindividuelle Hilfsmittel zu zertifizieren. Den Kernpunkt des „virtuellen Belastungstests“ bildet eine in Bezug auf die vorgeschriebene Normprüfung mit messtechnischen Methoden validierte numerische Simulation, die in die Software integriert ist. Durch den Abgleich der entstandenen Simulationsergebnisse, z. B. mit den Vorgaben einer existierenden Norm, werde über die Zulässigkeit der Design-Modifikation entschieden und so die Strukturfestigkeit des individualisierten Produkts sichergestellt. Dadurch gelinge es, die Anzahl der zeit- und kostenaufwändigen physikalischen Prüfungen zu minimieren. Da der Plattform-Betreiber für diese Schritte die Verantwortung übernimmt, müssen sich einzelne Nutzer der Plattform nicht damit auseinandersetzen.
Den beteiligten Projektpartnern biete das Projekt wiederum die Möglichkeit, weitreichendes Know-how in der Prozessdigitalisierung, von der digitalen Erfassung über die Konstruktion bis zur additiven Fertigung, aufzubauen. Die enge Verzahnung zwischen Industrie und Forschung sichere außerdem die Verwertung der Projektergebnisse in Form von Forschungs- und Lehraktivitäten, so die Partner.
Allerdings seien das Vorhaben und die einzelnen Arbeitsziele technisch höchst anspruchsvoll und mit erheblichen Entwicklungsrisiken vor allem im Bereich der virtuellen Produktprüfung verbunden. Hier werde sowohl technologisch als auch regulatorisch wissenschaftliches Neuland betreten. Die Anforderungen der Validierbarkeit von virtuellen Tests und deren Anerkennung durch die Behörden und Prüfstellen müssen unbedingt erfüllt werden. Um die möglichen Risiken für die Unternehmen zu reduzieren und die Beteiligung der Experten aus der universitären Forschung zu sichern, unterstütze das Bundesministerium für Forschung und Bildung das Projekt mit einem Förderanteil von 70 Prozent am Gesamtvolumen von 3,13 Millionen Euro.
David Hochmann, Ann-Katrin Carl, Lutz Schuppener, Franziska Glas, Manuel Opitz
Care Center Rhein-Ruhr GmbH zählt mit über 170 Mitarbeitern zu den großen Hilfsmittelversorgern im Ruhrgebiet. Mit starkem Fokus auf Sonderanfertigungen und die BG-Versorgung besteht auch eine überregionale Ausstrahlung. Es besteht eine umfangreiche Expertise im klassischen Orthesenbau sowie erste Erfahrung mit Scantechnologien, Modellierung und 3D-Druck. Das inhabergeführte Sanitätshaus Gäher verfügt über acht Niederlassungen und 53 Mitarbeiter mit regionalem Fokus im Münsterland. Für das Projekt ist insbesondere das umfangreiche Vorwissen im Bereich der Unterschenkelorthetik relevant. Die Anwendungspartner bringen zum einen die Praxisanforderungen in das Projekt ein und übernehmen zum anderen die Konzeption und Entwicklung von 3D-Druck-gerechten Orthesen zur exemplarischen Erprobung der digitalen Plattform. Ihnen kommt zudem eine besondere Rolle bei der abschließenden Bewertung der Praxistauglichkeit zu.Die Klinik für Allgemeine, Unfall und Wiederherstellungschirurgie am Klinikum der Universität München wird sich schwerpunktmäßig mit allen medizinischen Aspekten im Projekt befassen. Ziel ist, die medizinische Begleitung, Evaluierung und Validierung der innovativ hergestellten Orthesen. Insbesondere die Schnittstelle zum Anwender, zum Patienten und die Integration in klinische Workflows ist von entscheidender Bedeutung.Die vom Institut für Soziologie der TU Berlin durchgeführte sozialwissenschaftliche Begleitforschung hat sich zum Ziel gesetzt, die sich im Rahmen von SIGMA 3D ergebenden Risiken zu analysieren, sie den Projektpartnern zu kommunizieren und sie durch die reflexive Einbindung der Ergebnisse in die Technikgestaltung zu minimieren. Zudem sollen Chancen, beispielsweise in Form einer nutzerzentrierten Technikentwicklung, herausgearbeitet werden. Eine sozialwissenschaftliche Perspektive soll den Blick der einzelnen Projektpartner für die komplexen Zusammenhänge zwischen Technik und Gesellschaft schärfen und ihnen helfen, ihre Arbeit verantwortungsvoll zu gestalten.
- Dirk Treiber findet bei Enovis neue berufliche Heimat — 13. August 2025
- Rehavision – Netzwerken und Nachwuchs fördern — 2. Juli 2025
- Das Handwerk trauert um Werner Dierolf — 28. September 2024